Kalibrasyon
Kalibrasyon, dilimize Fransızcadan giren bu sözcük, Metroloji Bilimi içerisindeki tanımı; belirlenmiş koşullar altında bir ölçü aleti veya ölçme sisteminin gösterdiği veya bir ölçüt/ölçeğin ifade ettiği değerler ile, o sistemi ölçen/referans olarak değerleri bilinen cihaz/sistem arasındaki ilişkiyi oluşturan işlemler dizisi olarak tanımlanır. Kalibrasyon bir ölçme aleti veya düzeneğinin doğru sonuçlar verecek şekilde ayarlanması işlemi değildir. ⓘ
- Kalibrasyonun sonucu, ölçeğin, ölçü aletinin veya ölçme sisteminin hatasını kestirmeye, veya belirli bir skalanın işaretlerine değerler verilmesine olanak sağlar.
- Kalibrasyon işlemi başka metrolojik özellikleri de belirleyebilir.
- Kalibrasyon sonucu,kalibrasyon sertifikası veya kalibrasyon raporu adı verilen bir doküman ile kaydedilebilir. ⓘ
Özel ekipmanlarla, hassas olarak yapilip orijin kabul edilen referans cihaza uygunlugu, bir rapor veya sertifika ile kayit altına alınan ölçme aleti veya ölçüm cihazina ait bu belgelerin üzerinde, mutlaka aletin/cihazin marka, model, seri numarası ve sapma buyuklugu bulunur. Ayrıca, sertifikanın izlenebilirliğini takip edebilmek için, Rapor veya Sertifika numarası da içermektedir. ⓘ
- Kalibrasyon sonucu bazen, bir kalibrasyon faktörü veya bir kalibrasyon eğrisi şeklindeki bir dizi kalibrasyon faktörü olarak ifade edilebilir. ⓘ
Kalibrasyon işleminde, kalibre edilen ölçü aletinin hata miktarı, kendisinden daha yüksek doğruluk u (en az 10 kat), bir ölçü aleti referans alınarak belirlenir. Kalibrasyonda referans alınan ölçü alet(ler)inin kalibrasyon sertifikası üzerinden ulusal veya uluslararası temel referanslara izlenebilir olması gerekir. Böylelikle kalibre edilen ölçü aletinin de temel referanslara izlenebilirliği sağlanmış olur. ⓘ
Kalibrasyon işlemi bir deneysel çalışma olup, deneysel bir çalışmadan beklenen tüm gereklilikler karşılanmalıdır. Yani çalışmalar kontrollü bir ortamda, özenli ve yazılı çalışma alışkanlığına sahip eğitimli kişilerce yapılmalı, çalışmanın yapıldığı ortam özellikleri, kullanılan ekipman, uygulanan yöntem, ölçüm belirsizliği ve sonuçlar kalibrasyon raporunda belirtilmelidir. ⓘ
Kalibrasyon sonucu ölçü aletinin hatasının, kullanıldığı proses veya varsa ilgili standartlarda belirtilen limitlerin dışına çıktığı belirlenmişse bu hatanın ayarlanarak giderilmesine çalışılır. Ancak ayar sonrası kalibrasyonun tekrarlanması ve son durumun raporlanması zorunludur. ⓘ
Ölçü aletleri, ölçüm prensip ve teknolojileri ile kullanıma, bulunduğu ortam şartlarına bağlı olarak, etkilenirler ve zamanla yaşlanırlar. Bu nedenle belirli periyotlarla kalibrasyonun tekrarlanması gerekir. Söz konusu periyodlar deneyimli kullanıcılar tarafından cihaz özellikleri ve kullanım koşulları göz önüne alınarak belirlenmeli, periyodun sıklığı, kalibrasyon raporunda belirlenmelidir. ⓘ
Kalibrasyonun, kalite yönetim sistemlerinin bir beklentisi olmasının nedeni, işletmeler için bir ihtiyaç olmasındandır. Eğer işletme içinde bir büyüklüğü ölçme ihtiyacı varsa, orada kullanılan ölçü aletinin istenilen doğrulukta ölçüm yapıp yapmadığının belirlenmesi ihtiyacı da vardır. ⓘ
Ölçüm teknolojisi ve metrolojide kalibrasyon, test edilen bir cihaz tarafından sağlanan ölçüm değerlerinin, doğruluğu bilinen bir kalibrasyon standardı ile karşılaştırılmasıdır. Böyle bir standart, doğruluğu bilinen başka bir ölçüm cihazı, voltaj, ses tonu gibi ölçülecek miktarı üreten bir cihaz veya metre cetveli gibi fiziksel bir obje olabilir. ⓘ
Karşılaştırmanın sonucu aşağıdakilerden biriyle sonuçlanabilir:
- test edilen cihazda önemli bir hata kaydedilmemesi
- önemli bir hata kaydedilmiş ancak herhangi bir düzeltme yapılmamıştır
- hatayı kabul edilebilir bir düzeye getirmek için yapılan bir düzeltme ⓘ
Açıkçası, "kalibrasyon" terimi sadece karşılaştırma eylemi anlamına gelir ve herhangi bir müteakip ayarlamayı içermez. ⓘ
Kalibrasyon standardı normalde bir metroloji kuruluşu tarafından tutulan ulusal veya uluslararası bir standarda izlenebilir. ⓘ
BIPM Tanımı
Uluslararası Ağırlıklar ve Ölçüler Bürosu (BIPM) tarafından kalibrasyonun resmi tanımı aşağıdaki gibidir: "Belirlenen koşullar altında, ilk adımda, ölçüm standartları tarafından sağlanan ölçüm belirsizlikleri ile miktar değerleri ve ilgili ölçüm belirsizlikleri ile karşılık gelen göstergeler (kalibre edilen cihazın veya ikincil standardın) arasında bir ilişki kuran ve ikinci adımda, bu bilgiyi bir göstergeden bir ölçüm sonucu elde etmek için bir ilişki kurmak için kullanan işlem." ⓘ
Bu tanım, kalibrasyon sürecinin tamamen bir karşılaştırma olduğunu belirtmekte, ancak test edilen cihazın ve standardın doğruluklarını ilişkilendirmede ölçüm belirsizliği kavramını ortaya koymaktadır. ⓘ
Modern kalibrasyon süreçleri
Bilinen doğruluk ve belirsizliğe duyulan ihtiyacın artması ve uluslararası alanda tutarlı ve karşılaştırılabilir standartlara sahip olma ihtiyacı ulusal laboratuvarların kurulmasına yol açmıştır. Birçok ülkede, müşterinin cihazlarına kalibrasyon yoluyla izlenebilirlik sağlamak için kullanılacak birincil ölçüm standartlarını (ana SI birimleri artı bir dizi türetilmiş birim) koruyacak bir Ulusal Metroloji Enstitüsü (NMI) mevcut olacaktır. ⓘ
NMI, standartların en üst seviyesinden ölçüm için kullanılan bir cihaza kadar kesintisiz bir zincir oluşturarak o ülkedeki (ve genellikle diğer ülkelerdeki) metrolojik altyapıyı destekler. Ulusal Metroloji Enstitülerine örnek olarak İngiltere'deki NPL, Amerika Birleşik Devletleri'ndeki NIST, Almanya'daki PTB ve diğerleri verilebilir. Karşılıklı Tanıma Anlaşması imzalandığından bu yana, katılımcı herhangi bir NMI'dan izlenebilirlik almak artık çok kolay ve bir şirketin ölçümler için İngiltere'deki Ulusal Fizik Laboratuvarı gibi bulunduğu ülkenin NMI'sından izlenebilirlik alması artık gerekli değil. ⓘ
Kalite
Kalibrasyonun kalitesini artırmak ve sonuçların dış kuruluşlar tarafından kabul edilmesini sağlamak için kalibrasyonun ve müteakip ölçümlerin uluslararası olarak tanımlanmış ölçüm birimlerine "izlenebilir" olması arzu edilir. İzlenebilirliğin sağlanması, ulusal standartlar (ABD'deki NIST gibi), uluslararası standartlar veya sertifikalı referans malzemelerle doğrudan veya dolaylı olarak ilişkili bir standartla resmi bir karşılaştırma yapılarak gerçekleştirilir. Bu, devlet tarafından işletilen ulusal standartlar laboratuarları veya metroloji hizmetleri sunan özel firmalar tarafından yapılabilir. ⓘ
Kalite yönetim sistemleri, tüm ölçüm cihazlarının resmi, periyodik ve belgelendirilmiş kalibrasyonunu içeren etkili bir metroloji sistemi gerektirir. ISO 9000 ve ISO 17025 standartları, bu izlenebilir eylemlerin yüksek düzeyde olmasını gerektirir ve nasıl ölçülebileceğini belirler. ⓘ
Bir kalibrasyonun kalitesini iletmek için kalibrasyon değerine genellikle belirtilen bir güven seviyesine kadar izlenebilir bir belirsizlik beyanı eşlik eder. Bu, dikkatli bir belirsizlik analizi ile değerlendirilir. Bazı durumlarda makinelerin bozulmuş bir durumda çalıştırılması için bir DFS (Spesifikasyondan Sapma) gerekir. Bu her ne zaman olursa olsun, yazılı olmalı ve bir kalibrasyon teknisyeninin teknik yardımı ile bir yönetici tarafından yetkilendirilmelidir. ⓘ
Ölçüm cihazları ve aletleri, ölçmek için tasarlandıkları fiziksel büyüklüklere göre kategorize edilir. Bunlar uluslararası düzeyde değişiklik gösterir, örneğin ABD'de NIST 150-2G ve Hindistan'da NABL-141. Bu standartlar birlikte elektromanyetik radyasyon (RF probları), ses (ses seviyesi ölçer veya gürültü dozimetresi), zaman ve frekans (intervalometre), iyonlaştırıcı radyasyon (Geiger sayacı), ışık (ışık ölçer), mekanik büyüklükler (limit anahtarı, basınç göstergesi, basınç anahtarı) ve termodinamik veya termal özellikler (termometre, sıcaklık kontrolörü) gibi çeşitli fiziksel büyüklükleri ölçen cihazları kapsar. Her bir test cihazı için standart cihaz buna göre değişir, örneğin basınç göstergesi kalibrasyonu için bir ölü ağırlık test cihazı ve sıcaklık göstergesi kalibrasyonu için bir kuru blok sıcaklık test cihazı. ⓘ
Cihaz kalibrasyon istemleri
Kalibrasyon aşağıdaki nedenlerden dolayı gerekli olabilir:
- yeni bir cihaz
- bir alet onarıldıktan veya değiştirildikten sonra
- bir yerden başka bir yere taşınma
- belirli bir süre geçtiğinde
- belirli bir kullanım süresi (çalışma saatleri) geçtiğinde
- kritik bir ölçümden önce ve/veya sonra
- bir olaydan sonra, örneğin
- bir alet, kalibrasyonunun bütünlüğünü tehlikeye atabilecek bir şok, titreşim veya fiziksel hasara maruz kaldıktan sonra
- ani hava değişiklikleri
- gözlemler şüpheli göründüğünde veya cihaz göstergeleri vekil cihazların çıktılarıyla eşleşmediğinde
- Müşteri spesifikasyonu, cihaz üreticisi tavsiyesi gibi bir gereklilik tarafından belirtildiği şekilde. ⓘ
Genel kullanımda kalibrasyon, genellikle bir ölçüm cihazındaki çıktının veya göstergenin, uygulanan standardın değerine belirli bir doğruluk dahilinde uyacak şekilde ayarlanması sürecini içerdiği kabul edilir. Örneğin, bir termometre kalibre edilebilir, böylece gösterge hatası veya düzeltme belirlenir ve (örneğin kalibrasyon sabitleri aracılığıyla) ölçek üzerindeki belirli noktalarda gerçek sıcaklığı Celsius cinsinden gösterecek şekilde ayarlanır. Bu, cihazın son kullanıcısının algısıdır. Ancak çok az sayıda cihaz, karşılaştırıldıkları standartlarla tam olarak eşleşecek şekilde ayarlanabilir. Kalibrasyonların büyük çoğunluğu için kalibrasyon işlemi aslında bir bilinmeyenin bir bilinenle karşılaştırılması ve sonuçların kaydedilmesidir. ⓘ
Temel kalibrasyon süreci
Amaç ve kapsam
Kalibrasyon süreci, kalibre edilmesi gereken ölçüm cihazının tasarımıyla başlar. Tasarım, kalibrasyon aralığı boyunca "bir kalibrasyonu tutabilmelidir". Başka bir deyişle, tasarımın makul bir süre boyunca belirtilen çevresel koşullarda kullanıldığında "mühendislik toleransı dahilinde" ölçümler yapabilmesi gerekir. Bu özelliklere sahip bir tasarıma sahip olmak, gerçek ölçüm cihazlarının beklendiği gibi performans gösterme olasılığını artırır. Temel olarak kalibrasyonun amacı, ölçüm kalitesini korumanın yanı sıra belirli bir cihazın düzgün çalışmasını sağlamaktır. ⓘ
Frekans
Tolerans değerlerinin belirlenmesine yönelik kesin mekanizma ülkeden ülkeye ve endüstri türüne göre değişmektedir. Ölçüm ekipmanının üreticisi genellikle ölçüm toleransını belirler, bir kalibrasyon aralığı (CI) önerir ve çevresel kullanım ve depolama aralığını belirtir. Kullanan kuruluş genellikle bu özel ölçüm ekipmanının muhtemel kullanım seviyesine bağlı olan gerçek kalibrasyon aralığını atar. Kalibrasyon aralıklarının belirlenmesi, önceki kalibrasyonların sonuçlarına dayanan resmi bir süreç olabilir. Standartların kendileri önerilen CI değerleri konusunda net değildir:
- ISO 17025
- "Bir kalibrasyon sertifikası (veya kalibrasyon etiketi), müşteri ile mutabık kalınan durumlar haricinde, kalibrasyon aralığına ilişkin herhangi bir öneri içermemelidir. Bu gereklilik yasal düzenlemelerle değiştirilebilir."
- ANSI/NCSL Z540
- "...kabul edilebilir güvenilirliği sağlamak için belirlenen ve sürdürülen periyodik aralıklarla kalibre edilmeli veya doğrulanmalıdır..."
- ISO-9001
- "Geçerli sonuçlar elde etmek için gerekli olduğunda, ölçüm ekipmanı... belirtilen aralıklarla veya kullanımdan önce kalibre edilmeli veya doğrulanmalıdır..."
- MIL-STD-45662A
- "... kabul edilebilir doğruluk ve güvenilirliği sağlamak için belirlenen ve sürdürülen periyodik aralıklarla kalibre edilecektir... Önceki kalibrasyonların sonuçları kabul edilebilir güvenilirliği sürdürmek için böyle bir eylemin uygun olduğunu gösterdiğinde, aralıklar yüklenici tarafından kısaltılacak veya uzatılabilecektir." ⓘ
Gerekli standartlar ve doğruluk
Bir sonraki adım kalibrasyon sürecinin tanımlanmasıdır. Standart veya standartların seçimi kalibrasyon sürecinin en görünür kısmıdır. İdeal olarak standart, kalibre edilen cihazın ölçüm belirsizliğinin 1/4'ünden daha azına sahiptir. Bu hedefe ulaşıldığında, son ölçüm de 4:1 oranıyla yapıldığında, ilgili tüm standartların birikmiş ölçüm belirsizliğinin önemsiz olduğu kabul edilir. Bu oran muhtemelen ilk olarak ABD Savunma Bakanlığı metroloji programı şartnamesi olan MIL-STD-45662A'ya eşlik eden El Kitabı 52'de resmileştirilmiştir. Bu oran 1950'lerdeki başlangıcından, gelişen teknolojinin çoğu elektronik ölçüm için 10:1'i imkansız hale getirdiği 1970'lere kadar 10:1 idi. ⓘ
Modern ekipmanlarla 4:1 doğruluk oranını korumak zordur. Kalibre edilen test ekipmanı, çalışma standardı kadar doğru olabilir. Doğruluk oranı 4:1'den azsa, telafi etmek için kalibrasyon toleransı azaltılabilir. 1:1'e ulaşıldığında, yalnızca standart ile kalibre edilen cihaz arasında tam bir eşleşme tamamen doğru bir kalibrasyondur. Bu kapasite uyumsuzluğu ile başa çıkmanın bir başka yaygın yöntemi de kalibre edilen cihazın doğruluğunu azaltmaktır. ⓘ
Örneğin, üreticinin belirttiği doğruluk oranı %3 olan bir gösterge %4 olarak değiştirilebilir, böylece %1 doğruluk oranına sahip bir standart 4:1 oranında kullanılabilir. Gösterge %16 doğruluk gerektiren bir uygulamada kullanılıyorsa, gösterge doğruluğunun %4'e düşürülmesi nihai ölçümlerin doğruluğunu etkilemeyecektir. Buna sınırlı kalibrasyon denir. Ancak nihai ölçüm %10 doğruluk gerektiriyorsa, %3'lük gösterge asla 3,3:1'den daha iyi olamaz. O zaman belki de gösterge için kalibrasyon toleransını ayarlamak daha iyi bir çözüm olacaktır. Kalibrasyon 100 birimde gerçekleştirilirse, %1'lik standart aslında 99 ile 101 birim arasında herhangi bir yerde olacaktır. Test ekipmanının 4:1 oranında olduğu durumlarda kabul edilebilir kalibrasyon değerleri 96 ila 104 birim arasında olacaktır. Kabul edilebilir aralığın 97 ila 103 birim olarak değiştirilmesi, tüm standartların potansiyel katkısını ortadan kaldıracak ve 3,3:1 oranını koruyacaktır. Devamında, kabul edilebilir aralığın 98 ila 102 olarak değiştirilmesi, 4:1'den daha fazla bir nihai oranı geri getirir. ⓘ
Bu basitleştirilmiş bir örnektir. Bu örneğin matematiğine itiraz edilebilir. Gerçek bir kalibrasyonda bu süreci yönlendiren düşüncenin kaydedilmesi ve erişilebilir olması önemlidir. Kayıt dışılık, tolerans yığınlarına ve kalibrasyon sonrası teşhis edilmesi zor diğer sorunlara katkıda bulunur. ⓘ
Ayrıca yukarıdaki örnekte, ideal olarak 100 birimlik kalibrasyon değeri, tek noktalı bir kalibrasyon gerçekleştirmek için göstergenin aralığındaki en iyi nokta olacaktır. Bu, üreticinin tavsiyesi olabilir veya benzer cihazların halihazırda kalibre edilme şekli olabilir. Çok noktalı kalibrasyonlar da kullanılır. Cihaza bağlı olarak, sıfır birim durumu, yani ölçülen olgunun yokluğu da bir kalibrasyon noktası olabilir. Ya da sıfır kullanıcı tarafından sıfırlanabilir - çeşitli varyasyonlar mümkündür. Yine, kalibrasyon sırasında kullanılacak noktalar kaydedilmelidir. ⓘ
Standart ile kalibre edilen cihaz arasında kalibrasyonu etkileyebilecek özel bağlantı teknikleri olabilir. Örneğin, analog olayları içeren elektronik kalibrasyonlarda, kablo bağlantılarının empedansı sonucu doğrudan etkileyebilir. ⓘ
Manuel ve otomatik kalibrasyonlar
Modern cihazlar için kalibrasyon yöntemleri manuel veya otomatik olabilir. ⓘ

Örnek olarak, bir basınç göstergesinin kalibrasyonu için manuel bir işlem kullanılabilir. Prosedür, test edilen göstergeyi bir referans ana göstergeye ve ayarlanabilir bir basınç kaynağına bağlamak, göstergenin açıklığı boyunca belirli noktalarda hem referans hem de test göstergelerine sıvı basıncı uygulamak ve ikisinin okumalarını karşılaştırmak için birden fazla adım gerektirir. Test edilen gösterge, sıfır noktasının ve basınca verdiği tepkinin amaçlanan doğruluğa mümkün olduğunca yakın olmasını sağlamak için ayarlanabilir. Sürecin her adımı manuel kayıt tutmayı gerektirir. ⓘ
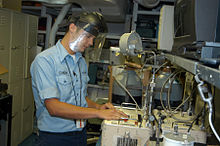
Otomatik basınç kalibratörü, bir elektronik kontrol ünitesini, Azot gibi bir gazı sıkıştırmak için kullanılan bir basınç yoğunlaştırıcıyı, bir hidrolik akümülatörde istenen seviyeleri tespit etmek için kullanılan bir basınç transdüserini ve sıvı kapanları ve gösterge bağlantı parçaları gibi aksesuarları birleştiren bir cihazdır. Otomatik bir sistem, kayıt tutma amacıyla veri toplanmasını otomatikleştirmek için veri toplama olanakları da içerebilir. ⓘ
Süreç tanımı ve dokümantasyonu
Yukarıdaki tüm bilgiler, belirli bir test yöntemi olan bir kalibrasyon prosedüründe toplanır. Bu prosedürler başarılı bir kalibrasyon gerçekleştirmek için gereken tüm adımları kapsar. Üretici bir tane sağlayabilir veya kuruluş, kuruluşun diğer tüm gereksinimlerini de kapsayan bir tane hazırlayabilir. Kalibrasyon prosedürleri için Amerika Birleşik Devletleri'nde Devlet-Endüstri Veri Değişim Programı (GIDEP) gibi takas merkezleri vardır. ⓘ
Bu kesin süreç, laboratuvarda en az belirsizliğe sahip ölçüm standartları olan transfer standartlarına, sertifikalı referans malzemelerine ve/veya doğal fiziksel sabitlere ulaşılana kadar kullanılan standartların her biri için tekrarlanır. Bu, kalibrasyonun izlenebilirliğini sağlar. ⓘ
Kalibrasyon sürecinin geliştirilmesi sırasında dikkate alınan diğer faktörler için Metroloji bölümüne bakın. ⓘ
Tüm bunlardan sonra, yukarıda tartışılan belirli tipteki münferit cihazlar nihayet kalibre edilebilir. Süreç genellikle temel bir hasar kontrolü ile başlar. Nükleer enerji santralleri gibi bazı kuruluşlar herhangi bir rutin bakım gerçekleştirilmeden önce "olduğu gibi" kalibrasyon verilerini toplar. Rutin bakım ve kalibrasyon sırasında tespit edilen eksiklikler giderildikten sonra "olduğu gibi" kalibrasyon gerçekleştirilir. ⓘ
Daha yaygın olarak, tüm süreç bir kalibrasyon teknisyenine emanet edilir ve başarılı bir kalibrasyonun tamamlandığını belgeleyen kalibrasyon sertifikasını imzalar. Yukarıda özetlenen temel süreç zor ve pahalı bir iştir. Sıradan ekipman desteğinin maliyeti, genel olarak kabul gören bir kural olarak, yıllık bazda orijinal satın alma fiyatının yaklaşık %10'udur. Taramalı elektron mikroskopları, gaz kromatograf sistemleri ve lazer interferometre cihazları gibi egzotik cihazların bakımı daha da maliyetli olabilir. ⓘ
Yukarıdaki temel kalibrasyon süreci açıklamasında kullanılan 'tek ölçüm' cihazı mevcuttur. Ancak, kuruluşa bağlı olarak, kalibrasyona ihtiyaç duyan cihazların çoğunun tek bir cihazda birkaç aralığı ve birçok işlevi olabilir. Yaygın bir modern osiloskop buna iyi bir örnektir. Tamamen kalibre edilecek 200.000 ayar kombinasyonu olabilir ve her şeyi kapsayan bir kalibrasyonun ne kadarının otomatikleştirilebileceği konusunda sınırlamalar vardır. ⓘ
Bir cihaza yetkisiz erişimi önlemek için genellikle kalibrasyondan sonra kurcalamaya dayanıklı mühürler uygulanır. Osiloskop rafının resmi bunları göstermektedir ve cihazın ayar elemanlarına yetkisiz erişimi mümkün kılacağından, cihazın son kalibrasyonundan bu yana çıkarılmadığını kanıtlamaktadır. Ayrıca son kalibrasyonun tarihini ve kalibrasyon aralığının bir sonraki kalibrasyonun ne zaman yapılacağını belirlediğini gösteren etiketler de vardır. Bazı kuruluşlar ayrıca kayıt tutmayı standartlaştırmak ve belirli bir kalibrasyon koşulunun ayrılmaz parçası olan aksesuarları takip etmek için her cihaza benzersiz bir kimlik atar. ⓘ
Kalibrasyonu yapılan cihazlar bilgisayarlarla entegre edildiğinde, entegre bilgisayar programları ve kalibrasyon düzeltmeleri de kontrol altında olur. ⓘ
Tarihsel gelişim
Kökenleri
"Kalibre etmek" ve "kalibrasyon" kelimeleri İngiliz diline Amerikan İç Savaşı gibi yakın bir tarihte, bir topun kalibresinin ölçülmesinden türetildiği düşünülen topçu tanımlarında girmiştir. ⓘ
Bilinen en eski ölçüm ve kalibrasyon sistemlerinden bazılarının Mısır, Mezopotamya ve İndus Vadisi'nin eski uygarlıkları arasında oluşturulduğu ve kazıların inşaat için açısal derecelendirmelerin kullanıldığını ortaya çıkardığı görülmektedir. "Kalibrasyon" terimi muhtemelen ilk olarak doğrusal mesafe ve açıların bir bölme motoru kullanılarak hassas bir şekilde bölünmesi ve yerçekimsel kütlenin bir tartı kullanılarak ölçülmesiyle ilişkilendirilmiştir. Yalnızca bu iki ölçüm biçimi ve bunların doğrudan türevleri, en eski uygarlıklardan yaklaşık MS 1800 yılına kadar neredeyse tüm ticaret ve teknoloji gelişimini desteklemiştir. ⓘ
Ağırlıkların ve mesafelerin kalibrasyonu (MS 1100 civarı)
İlk ölçüm cihazları doğrudan ölçüm yapıyordu, yani ölçülen miktarla aynı birimlere sahipti. Örnek olarak uzunluk ölçme çubuğu ve kütle ölçme tartısı verilebilir. On ikinci yüzyılın başında, I. Henry (1100-1135) döneminde, bir yardanın "Kral'ın burnunun ucundan uzanmış başparmağının ucuna kadar olan mesafe" olması kararlaştırıldı. Ancak, I. Richard (1197) dönemine kadar belgelenmiş kanıtlar bulamadık.
- Ölçülerin Ağırlığı
- "Krallığın her yerinde aynı büyüklükte bir metre olacak ve bu demirden olacaktır." 1100_CE) ⓘ
Sıvı ölçüleri için Magna Carta (1225) gibi diğer standardizasyon girişimleri, Fransa'dan Mètre des Archives ve Metrik sistemin kurulmasına kadar devam etti. 1100_CE) ⓘ
Basınçlı aletlerin ilk kalibrasyonu
En eski basınç ölçüm cihazlarından biri, Torricelli'ye (1643) atfedilen ve cıva kullanarak atmosferik basıncı okuyan cıvalı barometreydi. Kısa süre sonra su dolu manometreler tasarlandı. Tüm bunlar gravimetrik prensipleri kullanan doğrusal kalibrasyonlara sahipti ve seviyelerdeki fark basınçla orantılıydı. Normal ölçü birimleri uygun cıva veya su inçleri olurdu. ⓘ
Sağdaki doğrudan okunan hidrostatik manometre tasarımında, uygulanan Pa basıncı sıvıyı manometre U tüpünün sağ tarafından aşağı doğru iterken, tüpün yanındaki bir uzunluk ölçeği seviye farkını ölçer. Ortaya çıkan yükseklik farkı "H", atmosfer basıncına göre basınç veya vakumun doğrudan bir ölçümüdür. Fark basıncı olmadığında her iki seviye de eşit olur ve bu sıfır noktası olarak kullanılır. ⓘ
Sanayi Devrimi, manometreden daha pratik olan "dolaylı" basınç ölçüm cihazlarının benimsenmesine tanık olmuştur. Yüksek basınçlı (50 psi'ye kadar) buhar makinelerinde ölçek uzunluğunu yaklaşık 60 inç'e düşürmek için cıva kullanılıyordu, ancak böyle bir manometre pahalıydı ve hasara meyilliydi. Bu durum, Eugène Bourdon tarafından icat edilen Bourdon tüpünün kayda değer bir örnek olduğu dolaylı okuma aletlerinin geliştirilmesini teşvik etmiştir.
Sağdaki Bourdon göstergesinin önden ve arkadan görünümlerinde, alt bağlantı parçasına uygulanan basınç, düzleştirilmiş boru üzerindeki kıvrımı basınçla orantılı olarak azaltır. Bu, ibreye bağlı olan borunun serbest ucunu hareket ettirir. Cihaz, kalibrasyon standardı olacak bir manometreye karşı kalibre edilecektir. Birim alan baĢına düĢen dolaylı basınç miktarlarının ölçümü için kalibrasyon belirsizliği manometre sıvısının yoğunluğuna ve yükseklik farkını ölçme araçlarına bağlı olacaktır. Buradan inç kare başına pound gibi diğer birimler çıkarılabilir ve ölçek üzerinde işaretlenebilir. ⓘ